The textile printing and dyeing industry is a major contributor to industrial wastewater in China, ranking fifth in discharge volumes. Printing and dyeing wastewater, in particular, is a significant pollutant, placing second in discharge volume and fourth in total pollutants nationwide, accounting for over 70% of the textile industry's wastewater. Addressing the environmental challenges posed by this wastewater is critical. Despite the availability of various treatment technologies and solutions, the industry, known for its thin profit margins, continually seeks more efficient, cost-effective, and simple solutions.
To explore such advancements, WieTec Marketplace platform organized a unique "Printing and Dyeing Green Revolution" factory visit on April 24, 2024. This visit aimed to investigate innovative solutions from the perspective of end users.
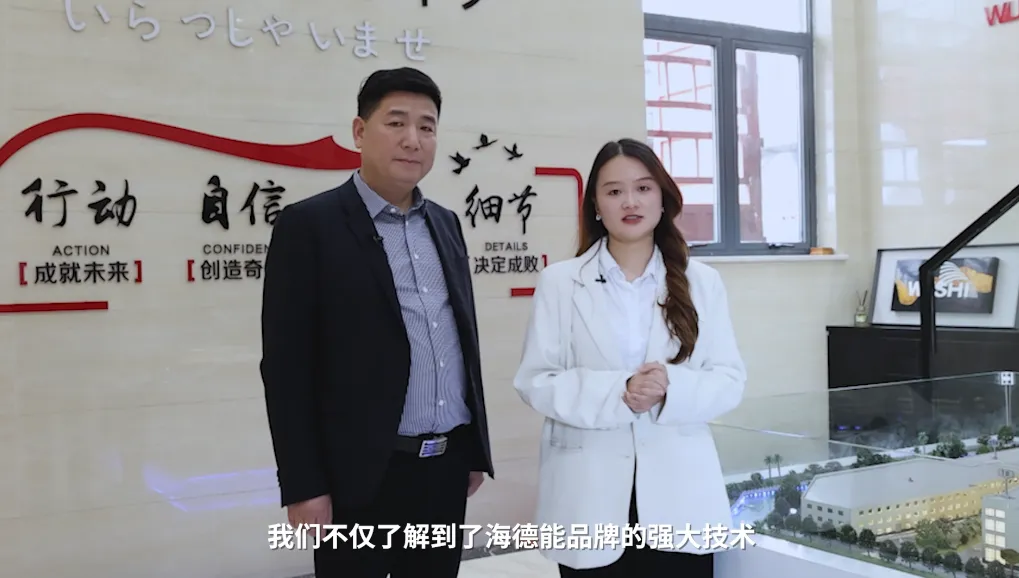
During this factory visit, we delved into the operations of corporate users to examine the revolutionary impact of zero wastewater discharge technology on the traditional printing and dyeing industry. The production process in this sector is characterized by large-scale water usage, leading to significant wastewater treatment challenges. This bottleneck has long hindered the green transformation of the industry. However, during our field visit, we witnessed firsthand how Wu's Printing and Dyeing Factory ingeniously addressed this issue, pioneering a new path for sustainable printing and dyeing.
This exploration not only highlights the potential of zero wastewater discharge technology but also underscores the importance of innovative solutions in driving the green revolution in the textile industry.
A Glimpse into Sustainable Innovation
Under the enthusiastic leadership of Chairman Wu Zhengxin, the factory visit team explored the Zero Liquid Discharge (ZLD) system workshop at Wu's Printing and Dyeing Factory. An unexpected sight captivated everyone's attention: several goldfish swimming leisurely in a large, clear tank, showcasing a harmonious blend of natural life and industrial manufacturing.
Mr. Wu smiled and explained, "The water used for breeding the goldfish comes directly from our zero discharge system. The water treated by our zero discharge equipment is 20 times cleaner than tap water." These words shattered the conventional perception of the printing and dyeing industry. Traditionally associated with toxic wastewater and unpleasant odors, the industry now demonstrated its potential to coexist with aquatic life. This striking image fueled our imagination about the possibilities of green, environmentally friendly, and sustainable development paths in industrial settings.
Venturing deeper into the core area of the workshop, we uncovered the secret behind the green transformation of the factory. A large, sophisticated piece of equipment was in operation, representing the factory's leap toward achieving zero wastewater discharge. Could this be the key to advancing the green transformation of the entire printing and dyeing industry?
Mr. Wu explained that this pioneering zero-emission equipment, capable of processing 500 tons per day, was introduced in 2022. Its first trial not only alleviated the immense pressure of traditional wastewater treatment but also achieved a 95% reuse rate of printing and dyeing wastewater. This significantly reduced the company's water costs, and the industrial salt produced through filtration added an additional revenue stream. The impressive recycling rate is attributed to the membrane treatment technology from Nitto Electric Hydraulics.
Nitto Electric's Minister Yamashiro, who accompanied us, provided an overview of the membrane technology's application in this large-scale zero-discharge treatment equipment. His insights gave our team a clearer understanding of the equipment's operating mechanism and highlighted the enormous potential and value of membrane technology in achieving zero wastewater discharge and water resource reuse.
This firsthand experience demonstrated the transformative power of advanced technology in promoting sustainable practices within the industry, reinforcing the importance of innovation in driving environmental progress.
The Future of the Green Revolution in Manufacturing
Our visit to Wu's Printing and Dyeing Factory was an impressive and inspiring experience. We witnessed the successful implementation of zero wastewater discharge technology and saw the remarkable efficacy of Nitto Electric's membrane technology in treating printing and dyeing wastewater. This visit underscored the critical importance of green printing and dyeing for the sustainable development of China's manufacturing industry.
With the continuous advancement and application of water treatment technology, we are optimistic that China's manufacturing sector will evolve to become cleaner, healthier, and more sustainable.
Hydra Energy Corporation of America
Since entering the reverse osmosis membrane (RO) field in 1970, Hydra Energy Corporation of America has become one of the most respected and experienced membrane product companies worldwide. Their products are used in various applications, including drinking water, boiler feed water, industrial process water, wastewater treatment, surface water treatment, seawater desalination, household water purification, electronic flushing water, agricultural irrigation, and pharmaceuticals. Visit the company store for more information. For further consultation, follow the official WeChat account of "Hydra Energy of America."
Company Factory Visit Activities
The factory visit activities initiated by WieTec Marketplace platform are excellent opportunities to promote exchanges between companies, enhance brand trust, and broaden market perspectives. We invite more companies to join this journey, explore industry frontiers together, share successful experiences, and collectively promote the prosperity and development of the environmental protection and energy-saving industry.
We believe that with the participation of more companies, these factory visit activities will become a powerful force driving the healthy development of the entire environmental protection and energy-saving sector. Let us move forward hand in hand, continue to grow through exploration and communication, and create a better future together!