At the National Science and Technology Awards Conference held in June this year, three projects related to membrane separation were honored. Membrane separation technology has a broad range of applications, and in the previous article (published last week), we explored its role in water treatment and gas purification. In this follow-up, we'll dive deeper into its applications in other areas and what the future holds for this innovative technology.
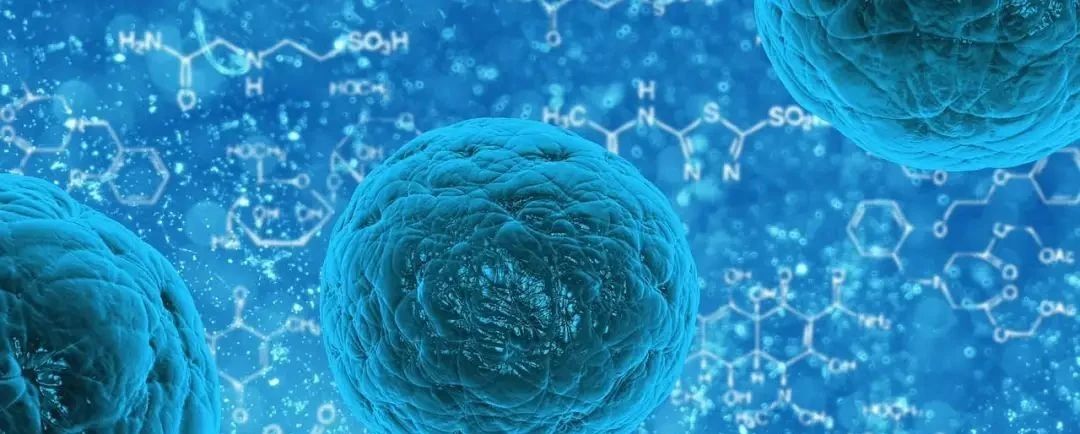
Membrane Separation in Biological Processes, Medicine, and Healthcare
One of the standout features of membrane separation is that it doesn't require acids, alkalis, organic solvents, or heat. This avoids chemical residues and protects sensitive components from damage, making it a highly effective solution for biological separation. As a result, membrane technology has found extensive use in making biological products safer and more efficient.
Revolutionizing Sugar Production
Take sucrose production, for example. Traditional methods like the carbonation or sulfite processes often leave behind unwanted substances, like sulfur dioxide, and generate significant waste. But membrane technology is changing that. In 2019, after five years of research, a team led by Wan Yinhua and Luo Jianquan from the Chinese Academy of Sciences collaborated with industry partners to produce the world's first batch of sugar using membrane separation.
This breakthrough brought remarkable improvements. The new process reduced costs by 100 yuan per ton of sugar, saved 20% in energy, and increased sugar yield per ton of cane by 20%. Most impressively, it achieved "zero discharge" of waste. This not only cut costs and raised profits but also drastically improved the environmental footprint of sugar production. The success of this project has led to its adoption in sugar factories across Guangdong, Guangxi, and Yunnan provinces, offering a new path forward for the sugar industry.
Membrane Technology in Biopharmaceuticals
Beyond sugar, membrane separation is gaining ground in the biopharmaceutical industry. It offers unique advantages for separating, concentrating, and purifying biological molecules like proteins, as well as in sterilization and virus filtration during drug production.
During the COVID-19 pandemic, the demand for vaccines, antibody drugs, and blood products surged. While there are many methods to separate and purify biological drugs, membrane technology plays a critical role in nearly every stage of the process. In upstream processes, membranes ensured the safety and stability of cell cultures. In contrast, in downstream processes, they were used for filtration, virus removal, and purification steps, improving both the safety and efficiency of drug production.
Hangzhou Cobetter Filtration Equipment Co., Ltd., a leader in membrane technology, has long been at the forefront of this field, offering comprehensive membrane solutions for producing vaccines, blood products, and other biopharmaceuticals. Their virus filtration membranes, crucial for ensuring the safety of these products, have become increasingly important.
Breaking Monopolies in Virus Filtration Technology
Before 2021, foreign companies like AsahiKasei Bioprocess, Millipore, and Sartorius monopolized the technology for virus filtration membranes. This dependency became especially concerning during the COVID-19 pandemic when supply chain disruptions posed a major threat. However, in 2021, Cobetter successfully launched its virus filtration membrane, ViruClear VF, breaking this monopoly. Other Chinese companies, such as Hangzhou Jiuling Technology and Saipu, have since followed suit, further advancing domestic capabilities in this critical field.
Life-Saving ECMO Systems
Membrane technology is also a key component in life-saving medical devices like the extracorporeal membrane oxygenation (ECMO) system. ECMO, which provides crucial support for patients with severe respiratory failure, has been vital during the COVID-19 pandemic. Before 2023, the market was dominated by foreign brands like Maquet, Medtronic, and Sorin. But in January 2023, Shenzhen Hannuo Medical Technology Co., Ltd. received approval for the first domestically produced ECMO device, marking a significant milestone for China.
In ECMO systems, the oxygenation membrane replaces the function of the lungs by supplying oxygen to the blood and removing carbon dioxide. These membranes must be highly efficient and reliable, with a unique structure to ensure safety. For years, the production of these specialized membranes, made from poly-4-methyl-1-pentene (PMP), was monopolized by 3M. However, ongoing efforts in China are working toward breaking this dependency as well.
Professor Wang Xiaolin and Associate Researcher Lin Yakai's Innovations in Oxygenation Membranes
Professor Wang Xiaolin and Associate Researcher Lin Yakai, from the Joint Research Center for Medical Membrane Materials at Tsinghua University’s Department of Chemical Engineering, in collaboration with Sinopec’s Beijing Yanshan Branch, have achieved significant breakthroughs in membrane technology.
Their team developed a semi-empirical method for screening diluents, which has resulted in a more efficient way to produce poly-4-methyl-1-pentene (PMP) membranes. These membranes feature a sponge-like structure that offers superior nitrogen permeability and anti-leakage performance compared to commercial PMP membranes. This innovation led to China’s first authorized patent in this specialized field, breaking the long-standing monopoly held by 3M in the United States.
However, since PMP resins are still imported, the team explored alternatives. They experimented with using polypropylene (PP), a cheaper, locally sourced material with better gas permeability, to create hollow fiber oxygenation membranes. By using a composite phase separation method, they successfully produced a PP membrane with gradient pores and a dense outer layer, providing performance close to PMP membranes. The Joint Research Center is now actively working on domestic production of both PMP and PP resins, making steady progress toward localization.
Bridging the Gap in Membrane Technology
While China has made significant strides in membrane separation, particularly in the development and production of mid to low-end materials, a clear gap remains between China and global leaders in high-end membrane technology. Several challenges still need to be addressed in areas like research and development, production processes, and market diversification.
High-end membranes require superior separation accuracy, anti-fouling properties, and long-term stability in demanding conditions such as chemical, thermal, and mechanical environments. Many domestic products still fall short of international standards. Additionally, China’s membrane production equipment lags in efficiency, precision, and consistency when compared to its advanced global counterparts.
Foreign companies, with decades of technical expertise and excellent after-sales service, have established strong trust and loyalty among customers. As a result, domestic membranes are mostly used in fields like industrial water and wastewater treatment, while market share in the high-end sector remains limited.
Overcapacity in Low-End Materials, Deficits in High-End
Similar to other industries, China faces an overcapacity of low-end membrane materials but hasn’t yet achieved domestic production of high-end alternatives. This imbalance stems largely from a disconnect between education, research, and industrial production.
In education, the knowledge system hasn’t evolved quickly enough to keep up with industry demands. Despite growing interest in membrane separation technology, its presence in undergraduate curricula is still limited. Most universities offer only elective courses, leaving students with a weak foundation in this critical field. However, there are signs of progress—Fuzhou University opened the country’s first dedicated Membrane Technology College in March 2024, a step toward filling this educational gap.
On the research front, more emphasis needs to be placed on practical applications. While progress has been made under policies aimed at shifting research priorities, much of the focus remains on publishing papers rather than solving real-world problems. The commercial transformation of research remains slow.
In production, the lack of standardized processes and quality control is a persistent issue. Domestic products often suffer from inconsistent quality due to insufficient compliance with international standards and limited use of automation and intelligent manufacturing technologies. Improving these areas would enhance product consistency and meet the demands of high-end applications. By implementing real-time monitoring, automated production controls, and data-driven process optimizations, manufacturers can boost efficiency and reduce costs.
Path Forward: Strengthening Collaboration and Focusing on Applications
To overcome these challenges, it’s essential to improve coordination between education, research, and industry while also fostering applied and forward-looking research.
Focus on applied research. While developing new membrane materials is vital, there’s also a need to optimize how membrane technologies are applied in practice. Enhancing the performance of membrane components, refining membrane processes, and exploring new applications will yield more immediate results. These efforts could open up more practical uses of membrane technology beyond just material innovations.
Invest in forward-looking research. China must move beyond following in the footsteps of global leaders and focus on breaking through critical "bottleneck" technologies. Current research often lacks groundbreaking or disruptive innovations. To maintain global competitiveness and avoid being constrained by foreign technologies, China must prioritize interdisciplinary collaboration and original innovations that push the boundaries of membrane materials, processes, and applications.
By prioritizing both applied and future-focused research, China can maintain technological autonomy and increase its presence in the global membrane market.