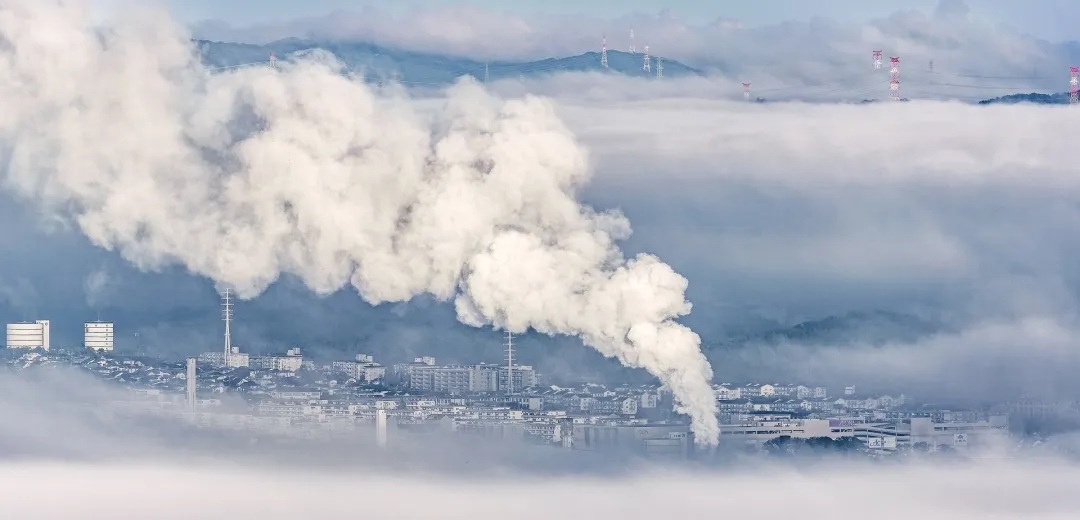
In the ever-evolving field of membrane separation technology, 2024 has been a landmark year. The National Science and Technology Awards Conference, held in June, recognized three groundbreaking projects in this domain, showcasing China's growing influence in environmental engineering and resource management:
Key Technology and Application of New Membrane Water Treatment won the prestigious First Prize for its advancements in water treatment technology.
Creation and Application of Gas Purification Membrane Materials earned the Second Prize, highlighting innovations in air purification.
Creation and Application of Drinking Water Safety Guarantee Technology System, a multi-faceted project using various membrane technologies, also secured a First Prize.
This is the first time membrane separation has received Three National Science and Technology Progress Awards in a single year—a testament to China's rising technical expertise. These accolades reflect the growing importance of membrane separation in environmental sustainability, resource recovery, and industrial processes.
What Makes Membrane Separation So Powerful?
Compared to traditional separation methods, membrane separation offers several significant advantages:
Energy Efficiency: Most processes occur at room temperature, requiring minimal energy as no phase change (except in cases like distillation) is needed.
Simplicity and Scalability: It allows concentration, purification, and separation in one step and can be scaled easily for both small- and large-scale operations.
Environmental Benefits: It’s a chemical-free, adaptable, and low-cost solution for numerous industries.
These attributes have led to its broad application across industries, from substance separation to detection, controlled release, and reaction control. Given its immense potential, membrane separation has long been prioritized by the Chinese government. During the "13th Five-Year Plan," 23 policy documents highlighted its importance, and new policies under the "14th Five-Year Plan" continue to push its advancement.
Membrane Separation in Water Treatment: Transforming the Industry
Water treatment remains the largest and most mature field for membrane separation, with desalination and drinking water purification as its flagship applications. This dominance explains why reverse osmosis membranes account for the highest market share in China and worldwide.
A standout project from this year’s awards, Key Technology and Application of New Membrane Water Treatment, includes major breakthroughs in ultrapure water separation membranes—critical in semiconductor manufacturing—and innovations in nuclear-contaminated water treatment. The successful localization of these advanced membranes, previously dominated by foreign companies, marks a major step forward for China’s technology sector.
For example, Chinese companies like Wharton Technology Co., Ltd. have developed their own ultrapure water membranes, the UE series, now used in multiple high-tech microelectronics projects. To further support this growth, the China Membrane Industry Association introduced several group standards in 2023, including:
Technical requirements for ultrafiltration membrane components for ultrapure water in the semiconductor industry (T/ZGM 011-2023),
Standards for spiral reverse osmosis membranes (T/ZGM 012-2023),
Electro-deionization membrane stacks (T/ZGM 013-2023).
These standards help domestic companies meet global benchmarks, drive product innovation, and promote the high-quality development of China’s membrane industry.
Wastewater Treatment: Turning Pollution Into Resources
Membrane separation technology is also revolutionizing wastewater and sewage treatment. With stricter environmental regulations in China, industries face immense pressure to treat wastewater effectively and at a low cost. The traditional dilemma of balancing treatment costs and environmental responsibility has pushed many enterprises toward illicit discharge practices to reduce financial burden.
However, when applied effectively, membrane separation can make wastewater treatment not just an environmental necessity but a profitable venture. Take, for instance, the "Membrane Preparation and Integration Technology for Zero Emission of Pulping Wastewater" project, led by Professor Xing Weihong under the guidance of Xu Nanping, a member of the Chinese Academy of Engineering. This project built the world’s first zero-emission demonstration for pulping wastewater, capable of processing 40,000 tons per day. It revitalized the Nantong Prince Papermaking project, which was on the brink of collapse, creating a 10-billion-yuan turnaround.
A more recent success is the fine chemical park in Ningxia’s Pingluo Industrial Park. Historically plagued by pollution, the park faced serious restrictions due to its inability to balance water demand and waste discharge. In response, China’s first zero-discharge project for wastewater treatment in a fine chemical park was launched in 2022-2023. The project, implemented by Meifeng Environment, employed advanced membrane separation to achieve full wastewater reuse without external discharge. The process converts brine into industrial-grade salts, which are reused in production, significantly reducing waste disposal costs.
The membrane system used in this project boasts a 98.6% recovery rate, reducing impure salt waste by 95% compared to traditional methods. This breakthrough enables the park to treat 10,000 tons of wastewater daily, meeting its production needs while reusing water for landscaping and urban utilities.
Gas Purification and Separation: Innovation Meets Efficiency
Beyond water treatment, membrane separation technology is making significant strides in gas purification, a crucial area for industries grappling with air quality and emissions. Traditional methods such as bag, cyclone, and electrostatic dust removal systems have long been used to manage dust, while adsorption, condensation, combustion, and chemical absorption techniques are employed to control volatile organic compounds (VOCs). However, these conventional technologies struggle to handle ultrafine dust and complex industrial waste gases effectively, especially when high resource recovery is needed. In contrast, membrane separation technology stands out as an energy-efficient, high-performance alternative, capable of meeting emission standards while enabling valuable resource recovery.
A prime example of this is the award-winning project "Creation and Application of Gas Purification Membrane Materials," led by Professor Jin Wanqin’s team from Nanjing Tech University’s State Key Laboratory of Materials Chemical Engineering. Their breakthrough innovations in membrane materials have set a new standard for removing ultrafine dust (at submicron levels) and organic compounds from industrial flue gases, while also recovering high-value-added powders and solvents.
Breaking Barriers in Gas Purification with Membrane Technology
Professor Jin’s team developed a novel design method for gas-solid separation membranes, establishing a link between membrane structure performance and control parameters. The gas purification membranes they created outperform international benchmarks, boasting over 30% higher air permeability and 198% better mechanical strength. These membranes can remove 99.99% of 0.3-micron ultrafine dust, far exceeding global standards.
A key challenge in industrial gas purification is oily aerosol contamination, which can create pollution layers on traditional filter materials, degrading their performance over time. To address this, the team introduced a heat-assisted in-situ functionalization method to make membranes both hydrophobic and oleophobic. This innovation allows for precise control over membrane bonding and wettability, resulting in a dual-repellent membrane that resists pollution and offers extended service life.
Real-World Applications and Economic Impact
The gas purification membranes developed by Professor Jin’s team are now widely used across industries. Over 200 projects, including those by major companies like Sinopec, Hengyi Petrochemical, and Jiangsu Huachang Chemical, have adopted this technology. These projects span 25 provinces and autonomous regions in China, making significant contributions to industrial waste gas treatment. The membranes are particularly effective in treating chlorine-containing gases and oil-laden smokes, areas where traditional technologies often fall short.
To date, this membrane technology has processed over 300 billion cubic meters of industrial gas, recovering high-value-added powders and organic solvents worth more than 1 billion yuan. The economic and environmental benefits have been substantial, demonstrating that membrane technology can not only clean industrial emissions but also turn waste into wealth.
How Gas Separation Membranes Work
Gas separation membranes operate on a simple principle: the difference in partial pressure on both sides of the membrane drives the separation of gas components. Different gas molecules permeate the membrane at varying rates. Faster molecules accumulate on the permeation side, while slower ones remain on the feed side, enabling the separation of mixed gases.
Compared to traditional methods like cryogenics, pressure swing adsorption, and chemical adsorption, membrane technology offers a range of advantages:
Room temperature operation: No need for extreme temperatures, making it more energy-efficient.
Simplicity and modularity: The equipment is straightforward and can be easily scaled up or adapted to various gas separation needs.
High efficiency: It’s capable of handling a wide variety of gases with impressive separation accuracy.
This versatile technology has found successful applications in several industries. For instance, it is used in hydrogen recovery within the ammonia synthesis industry, tail gas treatment in petrochemical processes, and oxygen and nitrogen enrichment systems. These real-world implementations have demonstrated the practical and economic viability of membrane separation for gas purification.
Helium: The "Golden Gas" Powering High-Tech Industries and China's Race for Self-Sufficiency
Helium, often called the "golden gas," plays a crucial role across a wide range of industries—from military applications and petrochemical processes to medical technologies, semiconductor manufacturing, and deep-sea diving. It’s an essential element in superconducting experiments and cryogenic refrigeration, making it a rare and strategic resource critical to global high-tech industries.
China, despite its enormous industrial scale, faces a helium scarcity, with over 95% of its helium supply dependent on imports. The country holds an estimated 1.1 billion cubic meters of helium, yet only about 50 million cubic meters are extractable—a mere 0.1% of global reserves. This heavy reliance on foreign imports has spurred urgent research into technologies that can tap into the low-concentration helium found in natural gas (helium content of just 0.1–0.3%) and dramatically reduce costs. If these resources can be harnessed efficiently, China could meet more than 40% of its helium demand domestically.
The Challenges and Solutions in Helium Extraction
Traditional methods of extracting helium, particularly cryogenic distillation, offer the advantage of producing high-purity helium but come with significant drawbacks. The high costs of production, massive equipment investment, and enormous energy consumption limit the scalability and efficiency of cryogenic methods. To overcome these challenges, researchers have been focusing on combining membrane separation technology with cryogenic distillation and pressure swing adsorption (PSA). This hybrid approach significantly reduces energy use and equipment costs while maintaining the ability to extract high-purity helium. As a result, it has become a key area of research and has already been successfully applied in several projects across China.
Breakthroughs in Domestic Helium Production
In November 2022, Sinopec made a major breakthrough by commissioning the first helium purification project in China’s southwest, located at the Fuling LNG Plant operated by Sinopec Chongqing Petroleum Branch. Notably, the helium purification membrane used in this project was developed entirely within China, marking a significant achievement in overcoming the technological barriers previously dominated by the United States and Japan in the field of polymer-based helium separation membranes. This milestone is a major step toward reducing China's dependency on foreign helium sources.
Another breakthrough came through the work of the China Coal Research Institute, which teamed up with Yaojie Coal and Electricity Group to develop an integrated process for extracting helium from coalbed methane. This process—combining pressure swing adsorption, membrane separation, and refining—achieved key technological advancements in helium extraction. The team successfully tackled the challenges of decarbonization and concentration of helium in multi-component coalbed methane, achieving helium purity levels exceeding 99.9999%. In 2023, the world’s first high-purity helium extraction facility for coalbed methane, with a capacity of 36,000 cubic meters per day, was brought online, further proving that China has fully mastered the complete process for helium extraction from coalbed methane.
Innovative Applications of Membrane Technology in Helium Extraction
At the beginning of 2023, the China Research Institute of Engineering Technology achieved another technological triumph by applying its hydrogen-helium separation and purification system to a natural gas flash gas (BOG) helium extraction project in Luliang, Shanxi. The system, which integrates cutting-edge BOG helium extraction technology using pressure swing adsorption, membrane separation, and adsorption dehydrogenation, has set a new standard for helium extraction. This innovative system not only separates and purifies helium with a purity of more than 99.999% but also produces high-purity hydrogen, with similar purity levels.
This new approach allows for rough separation, refining, and purification of helium at room temperature, offering both efficiency and flexibility. The project successfully demonstrated long-term, low-temperature operational stability, proving that these technologies are not only viable but scalable for industrial use.
The Future of Helium Extraction in China
As China pushes toward greater independence in sourcing strategic materials, breakthroughs in membrane separation technology for helium extraction will play a pivotal role. By integrating membrane systems with other advanced methods like cryogenic distillation and pressure swing adsorption, China has already started to make significant strides toward reducing its reliance on imports. These technologies hold the potential to transform China’s helium supply chain, allowing the country to tap into its own natural gas reserves to meet a substantial portion of its domestic helium needs.
In an era where helium is becoming ever more essential to cutting-edge industries—spanning aerospace, quantum computing, and even clean energy—China’s progress in helium extraction represents a significant step not just for its own industrial strategy but for the global high-tech landscape. As demand for this "golden gas" continues to rise, the combination of domestic innovation, advanced extraction techniques, and strategic foresight could position China as a future leader in the global helium market.